
Design & Engineering
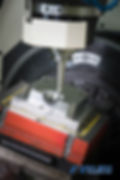
Experience Equals Wisdom
The success of any project starts here. Taking your challenging part geometry and incorporating it into an injection mold design becomes our main focus. We believe design intent with an eye towards efficiency, repeatability, and dependability of the mold is the key to success of your project.
As an innovative industry leader since 1985, we at M.R. Mold & Engineering continue to meet the needs of our customers' challenging product design concepts. With experience comes wisdom. Our track record of success allows us to design a tool that translates to reduced production costs. All our mold designs are created using Pro Engineer software. SolidWorks and AutoCad are also used to translate customer files to the Pro E platform. Pro E provides quick turnaround 2D design concepts for the proposed mold.

Some challenging part geometries require mold flow analysis to ensure well-define parting line and gate locations. M.R Mold has a seat of Moldex3D in-house to ensure that every design is optimized. As part of our “customer first” philosophy, no mold is released to production without your approval. We welcome your input during the mold design process, so that the mold will comply with your manufacturing and molding standards. Our management team is involved in every aspect of the design and mold build process, ensuring all is accomplished to meet on-time deliveries.
Flow Analysis
LSR system simulation is an essential tool for a complete part, mold and process optimization. The use of best-case and worst-case scenarios rules out costly real-world development trials. Our polymer system simulation greatly expands our engineering knowledge and quantitatively supports our decision-making process.

Our complete-simulation approach provides cost avoidance as well as cost savings. Like most forward-thinking companies, we at M.R. Mold & Engineering will change common development routines using a virtual process evaluation, in order to achieve smarter "lean manufacturing" goals.
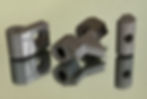
Metal 3D Printing
Our In-house Direct Metal Laser Sintering capability allows us to create stainless steel components for molds. We can print mold cores and inserts which have internal or complex geometry that would be difficult to machine using traditional methods. This allows us to print fully customized products!